[섬유제조공정 로봇자동화]
실증 사례(1) 여주티앤씨(도입기업)–하이젠RNM(공급기업)
◊참여 기업 개요
경북 경산에 위치한 여주티앤씨(대표 조연정)는 폴리에스터 복합사를 고객 맞춤 가공방식으로 생산하는 섬유기업이다. 합성섬유인 가연사, 열처리복합사를 비롯해 의류용 섬유, 리사이클 제품, 산업용(블라인드, 신발 등) 섬유 등 다양한 분야에 적용할 수 있는 섬유 제품을 생산하고 있다. 지난 2019년 소재·부품 전문기업과 강소기업에 선정됐으며, 2022년 수출의 탑 3백만불탑을 수상했다.
로봇SI업체인 하이젠RNM(구 하이젠모터)은 모터 전문기업으로, 제어기 부문에서 축적한 핵심 기술력을 바탕으로 2018년 로봇사업부를 신설, 부품 전문 기업에서 로봇 제조기업으로 변신했다. 이어 2020년 자체 개발한 로봇을 자동화 라인에 직접 적용하겠다는 전략 하에 로봇사업부 내에 로봇SI팀을 신설해 뿌리산업, 식음료 산업, 섬유산업 등 로봇 SI 사업을 확장하고 있다. 2021년 산업부 선정 소부장 정밀제어 부분 으뜸 기업으로 선정됐다.
◊대상 공정의 애로사항

▲ 여주티앤씨 대상 공정 흐름도
여주티앤씨의 제품 생산 프로세스는 원사 가공 후 원사 이송 → 원사 비닐 포장 → 원사 적재 → 원사 팔레트 래핑 포장 → 포장 완료 원사 배출의 순으로 이뤄진다.
대상 공정을 살펴보면, 작업자들은 하루 생산량 1만 7810kg을 기준으로 5kg 제품 3560여개를 일일이 저울에 올려 무게를 측정하고, 개별 비닐 포장을 박스에 넣는 과정을 반복적으로 수행한다. 이 때문에 작업자의 근골격계 질환 발생이 우려된다. 또한 5~6kg의 중량물 이동 시 허리를 숙였다가 펴는 동작을 반복적으로 수행하면서 낙하에 의한 찰과상, 요통 및 디스크 질환 등 안전사고 발생 우려도 있다. 육안 판정 방식으로 무게를 빠르게 측정하는 과정에서 무게 측정 오류가 생길 수도 있다. 이밖에도 제품 수출 시 균일한 품질 유지의 어려움, 개별 포장 작업시 오염 및 유해요소 발생 우려가 제기되고 있다.
◊ 실증 사업 추진
대상 공정에 로봇 자동화 라인을 구축하면, 근무자의 근골격계 질환을 초래하는 단순 반복 작업을 자동화하고, 기존 인력을 고부가가치 업무로 전환해 기술력을 제고하고, 저출산 및 고령화에 따른 노동 인구 감소에도 대처할 수 있을 것으로 기대된다. 공정 불량률 감소, 원가 절감 등 효과도 기대하고 있다.
여주티앤씨는 이번 실증 사업에서 원사 이송, 개별 비닐 포장 및 팔레트 적재, 포장/배출작업에 2022년 개발된 제품 픽업 이송 공정 모델과 제품 포장 공정모델을 도입했다. 원사 픽업이송 공정 모델은 로봇이 대차에서 원사를 픽업해 로딩/언로딩하고, 겐트리 시스템 및 트랜스퍼 장비를 통해 원사를 개별적으로 이송해 무게 측정 및 정렬 작업을 수행하는 픽업이송 자동화 시스템을 구축하는 것이다.
원사 포장 공정모델은 개별적으로 포장돼 있는 원사를 특수 제작된 멀티 그립퍼 장착 로봇을 이용해 원사 25개와 스티로폼 충진재, 총 4단의 원사 100개를 적재하는 것이다. 적재된 원사는 제품 출하를 위해 밴딩과 랩핑 후포장 공정으로 이동하고, 생산시 발생하는 유해요소를 차단하는 포장적재 자동화 시스템을 구축하는 것이다.

▲ 여주티앤씨-제품 픽업 이송 공정(원사 공급)
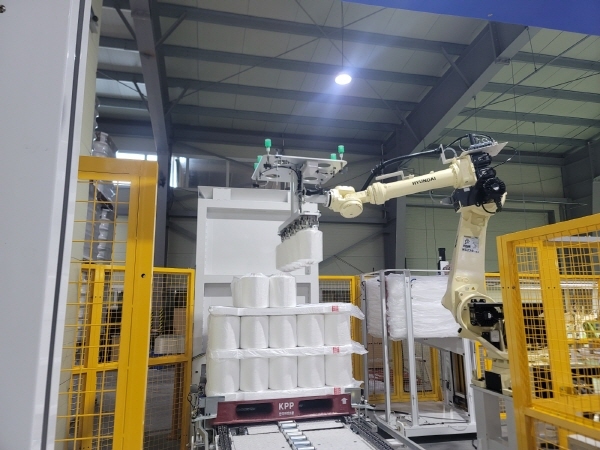
▲ 여주티앤씨-제품 포장 로봇자동화라인
공급기업인 하이젠RNM은 6축 다관절 로봇과 주변 장비들을 활용해 원스톱 라인을 구현했다. 제품 픽업 이송 라인에 원사 개별 무게 측정 장치와 개별 비닐 포장 장치를 설치해 무게 오측정과 비닐 포장 실수 불량을 줄였고, 제품 포장 라인에 멀티 그립퍼를 적용해 다수의 원사를 한번에 그립핑할 수 있도록 했다. 원사 픽업 이송 시스템에는 현대로보틱스의 가반하중 20kg 6축 다관절 로봇 2대와 주변장치를 설치했고, 원사 포장 시스템에는 현대로보틱스의 가반하중 220kg 6축 다관절 로봇 1대와 주변장치를 설치했다. 원스톱 라인 구축으로 원사 투입, 품질 검사, 적재, 포장 및 배출 작업을 모두 자동화하는 성과를 거뒀다.
◊ 기대효과
이번 실증 사업으로 공정 생산성이 현재의 하루 평균 1만 7810kg에서 2만kg으로 개선되고, 공정 불량률이 현재 3.13kg에서 2.47%로 낮아지는 효과를 거둘 수 있을 것으로 기대된다. 또한 이송 및 포장라인 투입 인원을 5명에서 3명으로 줄이고 납기 준수, 근로환경 개선, 신규 고객 확보 등도 가능해질 전망이다.
실증 사례(2) 대양, 한일첨단소재, 신한염직(도입기업) – 포원시스템(공급기업)
◊ 참여 기업 개요
경북 경산에 위치한 대양(대표 박상수), 한일첨단소재(대표 한용희, 차영한), 그리고 경기 시흥에 위치한 신한염직(대표 문창용)은 공급기업인 포원시스템과 협력해 실증사업을 진행했다.
대양은 1998년 회사 창립 이후 산업계에서 다각도로 활용되고 있는 HDPE 재질의 망을 제조해 95% 이상 수출하고 있다. 2017년과 2018년 스마트공장 구축 지원 사업을 통해 원단 포장시스템 구축 등을 지원받았다. 지속적으로 생산자동화 라인 구축에 힘쓰고 있으며, 스마트공장 구축과 로봇자동화 시스템 도입을 통해 생산성 및 제품 품질 향상, 고강도 작업환경 개선을 꾀하고 있다.
한일첨단소재는 K2, 네파, 블랙야크, 아디다스, 코오롱스포츠 등 다양한 스포츠웨어 업체에 원단을 공급하고 있다. 특수/방수 필름 라미네이팅, TPU코팅, 재귀반사 프린팅 등 기능성 원단을 주로 생산하고 있다. 경기도 시흥에 위치한 신한염직은 지난 1993년 설립되었으며, 경편 스판 벨벳을 시작으로 의류와 침구류에 들어가는 폴리에스터 제품을 생산하고 있다.
신한염직은 지난 1994년 설립이후 직물, 편조 원단 및 의류복 염색 가공 사업을 해왔으며 텐터기, 래피드 염색기, 로터리 와샤, 해포기 등 설비를 갖추고 있다. 2019년 스마트공장 고도화를 통해 염색 실험실에서 염액 자동피페팅 시스템과 컬러샘플관리시스템을 도입했다.
로봇SI기업인 포원시스템은 2008년 설립됐으며 자동화 시스템과 산업용 로봇을 활용해 생산공정 모니터링에서부터 제어까지 스마트팩토리 구축을 선도하는 기업을 목표로 하고 있다. 섬유산업과 염색산업을 시작으로 화학, 페인트, 화장품 등 다양한 산업에서 시스템 구축 실적을 확보하고 있다. 자동화 시스템, 로봇 제어 시스템, 모니터링 시스템 등 솔루션을 갖추고 있으며, 최근 디지털트윈 및 AI기술 개발에 힘을 기울이고 있다.
◊ 대상 공정의 애로사항

▲ 대양 공정 흐름
3개 기업의 제조 프로세스는 원단 가공 및 검사 후 원단 롤 포장기 투입 → 원단 롤 비닐 포장 → 원단 롤 이송 → 원단 롤 팔레트 적재 순으로 이뤄져 있다. 원단 이송 및 적재 공정(원단 투입-포장-원단 이송-원단 분리-원단 적재-원단 정리)의 가장 큰 문제점은 무거운 원단을 들고 옮기는 작업을 작업자가 직접 수행하고 있어, 작업 피로도가 높으며, 작업자 근골격계 손상을 유발할 수 있다는 것이다. 무거운 원단의 경우 2명 이상의 작업자가 공정에 투입되는데, 많은 인력 투입으로 작업 효율성이 떨어진다. 작업자 실수로 원단을 다른 팔레트에 적재하는 경우 해당 원단을 다시 찾는데, 시간이 오래 걸린다. 게다가 잘못된 원단 배송으로 인해 기업 이미지가 실추될 수 있다. 작업자가 직접 운반하던 원단 롤을 산업용 로봇으로 대체하면 작업환경을 개선할 수 있으며, 안전사고도 예방할 수 있다.
◊ 실증 사업

▲ 대양-원단 롤 픽업 공정

▲ 신한염직-원단 롤 픽업 및 이송 공정

▲ 한일첨단소재-원단 이중 포장 투입 공정
이들 수요 기업과 로봇SI기업인 포원시스템은 실증 사업을 위해 원단 롤 이송 및 팔레트 적재 작업에 2019년 개발된 원단 롤 이송 공정모델을 도입했다. 원단 롤 이송 공정모델은 작업자가 직접 이송/적재하던 해포공정에 로봇 시스템을 도입해 자동으로 원단을 이송 및 적재할 수 있는 시스템을 구현하는 것이다. 원단은 팔레트에 적재된 상태로 입고되는데, 비전 카메라 시스템을 통해 원단 배열을 확인하고 해포기에 원단을 투입해야한다. 원단 포장 및 적재 공정에 커스터마이징하여 적용한 모델은 산업용 로봇과 전용 그립퍼가 포장이 완료된 원단 롤을 팔레트에 적재하고 원단을 정리한다. 원단 적재시 원단별, 바이어별, 아이템별 팔레트로 구분해 적재하고 정리하는 작업을 수행한다. 적재 팔레트 개수는 현장 상황에 맞춰 다양한 배치가 가능하고 레일을 이용해 로봇이 이동하면서 적재한다. 포장 현황은 모니터링 프로그램을 통해 1일 포장 수량을 실시간 확인 가능한 시스템 구축을 목표로 하고 있다.
공급기업인 포원시스템은 다관절 로봇을 도입해 원단 롤 이송, 적재 공정을 자동화했다. 검사를 마친 원단 롤은 원단 롤 이송 시스템의 컨베이어를 통해 포장기로 이송되고, 이송된 원단 롤은 라이다 센서를 통해 인식된다. 이어 자체 개발한 전용 그립퍼로 파지 후 팔레트에 적재한다. 원단 롤 이송 시스템은 현대로보틱스의 가반하중 200kg~500kg 6축 다관절 로봇을 도입해 활용했다. 이 로봇을 활용해 70kg~120kg의 원단 롤을 팔레트에 정렬 및 적재할 수 있다.
◊ 기대효과
이번 실증사업을 통해 대양은 공정 생산성을 현재의 하루 평균 1만 4401kg에서 1만 5000kg으로 개선하고, 공정 불량률을 현재의 5%에서 4.5%로 낮추는 것을 목표로 하고 있다. 작업자도 현재 3명에서 2명으로 줄이고, 사이클 타임 개선, 근로 개선, 신규 고객 확보 등을 기대하고 있다. 한일첨단소재는 공정 생산성을 현재 하루 평균 9379yd에서 9800yd로 개선하고, 공정 불량률을 현재 5.2%에서 4.8%로 낮추는 것을 목표로 하고 있다. 작업자도 현재 3명에서 2명으로 줄일 수 있다. 사이클 타임 개선, 근로 개선, 신규 고객 확보도 기대하고 있다. 신한염직은 공정 생산성을 현재의 하루 평균 1만 8844yd에서 2만yd로 개선하고, 공정 불량률을 현재의 7.63%에서 6.50%로 낮추고, 작업자도 현재의 3명에서 2명으로 줄인다는 목표다. 사이클 타임 개선, 근로 개선, 신규 고객 확보 등을 기대하고 있다.
한발 더 나아가 참여기업들은 섬유 산업의 로봇 도입 성공 사례 실증 확산을 통해 해외 진출 공장의 리쇼어링 효과도 거둘 수 있을 것으로 기대하고 있다. <끝>
장길수 ksjang@irobotnews.com
<저작권자 © 로봇신문사 무단전재 및 재배포금지>
'산업용로봇' 카테고리의 다른 글
ABB, 볼보 전기차 생산라인에 로봇 1300대 공급한다 (1) | 2023.12.20 |
---|---|
화낙 미국법인, 산업용 로봇 'M-710iD/50M' 선봬 (1) | 2023.12.20 |
ABB, 산업용 6축 로봇에 '위자드 이지 프로그래밍' 지원 (1) | 2023.12.05 |
일본 미쓰비시전기, '2023 국제로봇전'에 산업용 로봇 신제품 출품 (0) | 2023.11.28 |
ABB, 산업용 스카라 로봇 신제품 'IRB 930' 출시 (1) | 2023.11.27 |