한국로봇산업진흥원(전담기관)과 한국생산기술연구원(지정 참여기관)은 제조산업의 경쟁력 제고를 위해 제조로봇 선도보급 실증사업과 제조로봇 플러스 실증 사업을 적극 추진해오고 있다. 제조 로봇 실증 사업은 표준공정모델을 기반으로 이뤄지고 있다. 표준 공정 모델을 기본으로 하되, 개별 사업장 또는 공정의 특성에 맞게 일부 모델을 수정해 로봇시스템을 구축한다.
한국로봇산업진흥원은 로봇 확산이 필요한 제조업종을 중심으로 167의 로봇공정 모델을 개발하고, 2024년 첨단 제조로봇 실증사업 등을 추진하고 있다.
한국생산기술연구원은 지난해 뿌리 분야와 바이오ㆍ화학 분야, 그리고 로봇-장비 연계 분야 수요 조사 및 공정 분석을 바탕으로 새로운 표준공정 모델을 개발했다. 이들 표준 공정 모델은 향후 추진 예정인 제조로봇 실증 사업에 적용될 예정이다. 지난해 개발된 주요 표준 공정 모델에 대해 살펴본다.(편집자)
◆ 뿌리분야 표준공정 모델
◊ 용접품 후처리 가공공정
‘용접품 후처리 가공공정’은 특장차, 자동차, 금속 제조 등의 분야에서 용접부 사상, 용접변형 보정, 열처리 등의 용접품 후처리 가공 공정에 다관절 로봇을 투입하여 용접품의 후가공 품질의 재현성 확보, 생산성 향상 및 생산비 절감, 산업재해 감소 등을 실현하는 공정이다.
이 공정 개발이 필요한 이유는 수작업에 의한 작업 효율과 생산성 저하, 후처리 품질 편차, 작업자 안전사고 위험, 근골격계 질환 등 열악한 작업 환경, 생산라인 전문인력 부족 등 문제가 있기 때문이다. 표준공정 모델과 실증 사업을 통해 용접품 후처리 가공 품질 향상, 후가공 품질 균일화, 불량률 감소, 생산비 및 단가 절감, 작업효율 및 생산성 향상, 작업효율 및 생산성 향상 등 효과를 기대할 수 있다.
이 표준공정 모델의 핵심 기능은 ▲용접 후처리 가공 공정(용접부 사상, 용접변형 보정, 열처리, 세정 등)의 로봇 자동화를 위한 하위 요소 기술 ▲용접 후처리 가공 공정 구현 및 실증을 위한 시스템통합(system integration) 기술 ▲용접 공정, 용접부 검사 공정, 이송/적재 공정 등과의 연계 ▲공정 중 발생 가능한 위험 요인으로부터의 보호 장치/시스템 등이다.
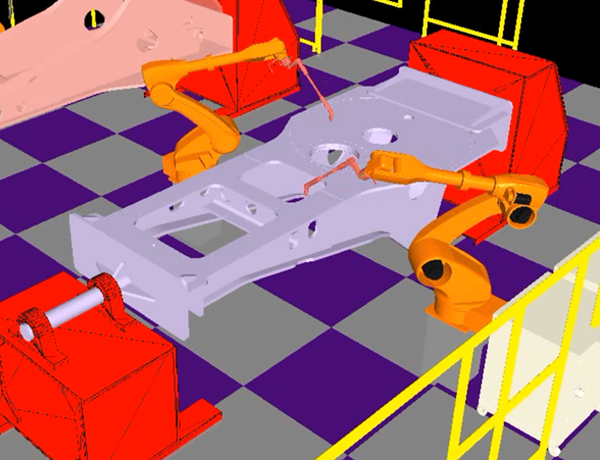
▲로봇시스템의 레이아웃
표준 공정 모델의 로봇자동화 시스템은 자동 용접 후처리 가공(화염 곡직) 로봇, 화염 곡직용 포지셔너, 후처리 가공 제어 판넬, 아크 용접용 로봇, 용접용 포지셔너, 용접 제어 판넬, 안전펜스 등으로 이뤄져 있다.
작업은 호이스트를 이용하여 용접품 이송 및 로딩 → 용접품을 포지셔너에 장착 및 고정 → 로봇에 의한 자동 아크 용접 → 로봇에 의한 용접 후처리(화염 곡직, 용접 변형 보정) → 용접부 검사(수작업 또는 로봇) → 후가공 완료품의 이송 및 배출/적재 등 순으로 진행된다.
◊ 도금품 로딩/언로딩 공정
도금품 로딩/언로딩 공정은 제품의 투입 과정에서 비전시스템을 통해 정렬 사항을 확인하고 다관절 로봇을 투입하여 로딩과 언로딩을 실행하고 생산성 향상 및 생산비 절감 등을 실현하는 공정이다
이 공정 개발이 필요한 이유는 고중량 단순 반복 작업으로 작업자의 근골격계의 질환 및 교체가 자주 발생하고, 도금 부품의 수요 증가로 인한 생산성 제고가 요구되고 있기 때문이다. 고중량 반복작업으로 인한 작업자의 집중력 저하로 생산성 및 품질 하락, 고중량 제품 취급중 작업자 피로도 증가로 인한 안전사고 발생 가능성도 공정 개발이 필요한 이유로 꼽힌다. 로봇시스템의 도입으로 생산 단가 절감, 검사 정확성 제고, 생산성 향상, 투입 인원 절감, 근무 환경 개선과 안전한 작업장 구현 등 효과를 기대하고 있다.
이 표준공정 모델의 핵심 기능은 ▲제품 로딩 및 언로딩 ▲투입라인에서 비젼을 통한 제품 정렬 ▲이동대차 자동이동 등이다.

▲로봇시스템의 레이아웃
표준 공정 모델의 로봇자동화 시스템은 6축 다관절 로봇, 그리퍼, 제어반(PLC), 로봇 베이스, 비전시스템, 작업자 보호 안전장치 등으로 구성돼 있다.
작업은 작업자가 제품 투입구에 제품 투입 → 투입구를 통해 컨베이어 벨트로 제품이 이동해 비전 설비 통과 → 비전 설비를 통해 제품 위치 및 모양 확인 → 로봇1을 통해 행거에 제품 로딩 → 이동대차를 통해 자동 도금장치 투입구로 이동 → 자동화 설비를 통한 도금 진행 → 도금이 완료된 행거를 이동대차를 통해 언로딩 위치로 이동 → 로봇2를 통해 퇴출 컨베이어에 언로딩 → 작업자가 회수하여 검사부로 이동 등 순서로 진행된다.
◊ 빈피킹 머신텐딩 정밀가공 공정
빈피킹 머신텐딩 정밀가공 공정은 임의 형상의 비정렬된 소재를 대상으로 3D 비전을 이용하여 각 소재의 위치와 자세 정보를 획득한 후 다관절 로봇을 이용해 소재를 잡고(Picking) 공작기계에 투입한 후 회수하는 공정 혹은 팔레트에 소재를 적재하는 공정이다.
이 공정 개발이 필요한 이유는 ▲수작업 기반 병목현상으로 작업효율 저하 및 생산성 악화 ▲작업자의 숙련도 차이에 따른 후가공 품질 편차 발생 ▲작업자 안전사고 위험, 근골격계 부담 등 열악한 작업 환경 ▲고숙련 작업자 수급 어려움 ▲단순 반복 작업의 연속으로 근골격계 이상 등 우려가 있기 때문이다. 로봇시스템 도입으로 작업자 근골격계 질환 예방, 가공 품질 균일화, 불량률 감소, 생산비 및 단가 절감, 작업 효율 및 생산성 향상 등 효과를 기대할 수 있다.
이 표준공정 모델의 핵심 기능은 ▲공작기계용 원소재의 로딩/언로딩, 이송, 적재 ▲3D 비전 기반 이미지 처리를 통한 각 소재의 픽킹 좌표 및 자세 획득 ▲획득 데이터를 로봇 제어기로 전달하여 로봇 구동 ▲적절하게 설계, 혹은 선정된 엔드이펙터를 이용하여 소재를 잡고 원하는 위치(공작기계 내부, 혹은 팔레트)로 이송 등이다.
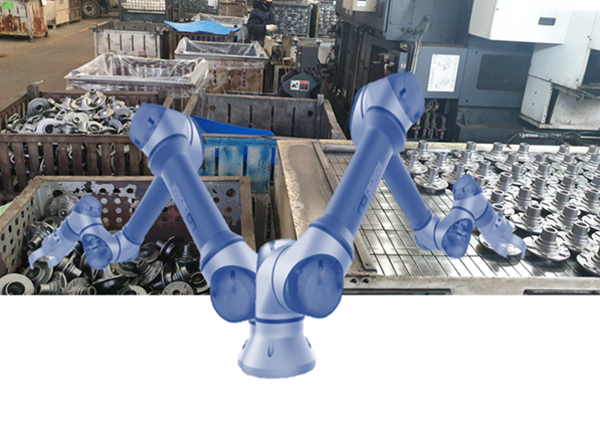
▲ 공정에 도입할 로봇시스템
표준 공정 모델의 로봇자동화 시스템은 6축 수직다관절 로봇, 그리퍼, 3D 비전, 로봇베이스, 제어반 등으로 구성된다. 작업은 혼합된 소재 공급 → 소재 판별 및 정렬 → 소재의 설비 로딩 및 가공 → 가공 완료후 언로딩 → 후가공 완료품의 이송 및 배출/적재 등 순으로 진행된다.
◊ 사출 후 조립, 검사, 적재 자동화 공정
사출 후 조립, 검사, 적재 자동화 공정은 플라스틱 사출 공정에서 사출 후 조립, 검사, 완제품 적재 등의 작업을 기존의 수작업에서 로봇시스템을 도입해 자동화하는 공정이다.
이 공정 개발이 필요한 이유는 ▲수작업에 따른 제품 제조 생산성 및 품질 저하 ▲수작업 조립 및 검사 시 발생되는 휴먼 에러 및 불량으로 인한 품질 저하 ▲현장 작업자에 의한 공정 불량 발생 ▲수작업에 따른 작업자 재해 및 안전 문제 등이 우려되기 때문이다. 로봇의 도입으로 생산성 향상, 공장 불량률 개선, 작업 환경 개선, 원가 경쟁력 확보, 노동자 만족도 향상 등 효과를 기대할수 있다.
표준공정 모델의 핵심 기능은 ▲사출품의 로딩/언로딩, 이송, 배출 ▲사출품의 조립 공정 ▲사출품의 품질 검사 ▲제품의 버, 파팅라인, 게이트 절단 등의 후공정 ▲트레이 안착 및 박스 이적재 공정 등이다.

▲로봇시스템의 레이아웃
표준 공정 모델의 로봇자동화 시스템은 6축 협동 로봇, 그리퍼, 제어반, 디버링 장치, 사출기, 비전시스템, 컨베이어시스템, 검사장치, 안전시스템 등으로 구성돼 있다. 작업은 피사출 제품 로딩 → 정렬 → 제품 로딩/언로딩 → 후가공(버, 게이트, 파팅라인 제거 및 정리) → 조립 및 융착 → 검사 → 트레이/박스 공급 → 적재 등 순서로 진행된다.
◊ 주조품 사상 후 검사 공정
주조품 사상 후 검사 공정은 주조품 생산 후 트리밍, 사상 공정 후 제품의 휨, 기준 홀(HOLE) 등 관리에 필요한 데이터를 확보하기 위하여 검사하는 공정이다.
이 공정 개발이 필요한 이유는 ▲작업자의 근골격계 및 안전사고 위험 ▲수작업 교정으로 대량 불량 발생 ▲수작업에 따른 병목현상으로 작업효율 저하 및 생산성 악화 ▲작업자의 숙련도 차이에 따른 후가공 품질의 편차 발생 ▲고숙련 인력수급 어려움 ▲소재의 종류(알루미늄)에 따라 사상 후 검사 및 수작업 교정시 발생하는 파편, 먼지 비산으로 열악한 작업 환경 노출 등 우려가 있기 때문이다. 로봇시스템 도입으로 ▲주조품 사상 검사 품질 향상 ▲검사 품질 균일화, 불량률 감소 ▲생산비 및 단가 절감 ▲작업효율 및 생산성 향상 ▲작업자 안전사고 위험 방지 및 근골격계 질환 예방 등 효과를 기대할 수 있다.
표준공정 모델의 핵심 기능은 ▲주조품의 로딩/언로딩, 이송, 배출 ▲주조품의 위치 인식을 위한 지그 장착/고정 ▲3기종 이상의 그립이 가능한 그리퍼 ▲검사 데이터 DB화와 육안으로 확인할 수 있는 HMI 구성 등이다.
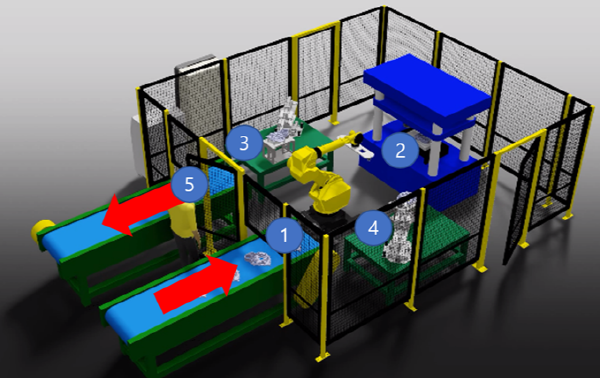
▲ 로봇시스템의 레이아웃
표준 공정 모델의 로봇자동화 시스템은 가반하중 50kg 제조 로봇, 3 기종의 소재를 그립 가능한 공용화 그리퍼, 검사 지그, 주조품 공급/이송 장치, 제어기, 안전장치 등으로 구성돼 있다.
작업은 주조품 이송/투입(컨베이어) → 주조품 프레스(교정) 취출&투입(로봇) → 검사기 취출&투입(로봇) → 주조품 이송/배출/적재(컨베이어) 등 순으로 이뤄진다.
◊ 중력주조품 후가공 사상공정
중력주조품 후가공 사상공정은 중력주조품의 후가공 사상 과정에 다관절 로봇을 투입하여 후가공 품질의 재현성 확보, 생산성 향상 및 생산비 절감 등을 실현하는 공정이다.
이 공정 개발이 필요한 이유는 ▲고중량, 중대형 형상에 따른 취급 어려움 ▲수작업 기반 병목현상으로 작업효율 저하 및 생산성 악화 ▲작업자의 숙련도 차이에 따른 후가공 품질의 편차 발생 ▲고숙련 인력수급 어려움 ▲소재의 종류(주철, 주강, 비철)에 따라 후가공 시 발생하는 파편, 용탕 및 흄, 먼지 비산으로 열악한 작업 환경 노출 등 우려가 있기 때문이다. 로봇자동화 시스템 도입으로 ▲중력주조품 후가공 품질 향상 ▲후가공 품질 균일화, 불량률 감소 ▲생산비 및 단가 절감 ▲작업효율 및 생산성 향상 ▲작업자 안전사고 위험 방지 및 근골격계 질환 예방 등 효과를 기대할 수 있다.
표준공정 모델의 핵심 기능은 ▲주조품의 로딩/언로딩, 이송, 배출 ▲주조품의 압탕부 등 불필요 부위 위치 인식을 위한 지그 장착/고정 ▲주철, 주강, 비철계 소재 종류에 따른 적절한 사상 툴 선정 및 개발 ▲가공 중 발생하는 파편, 용탕액적, 비산먼지 등으로부터 보호장치/시스템 마련 등이다.
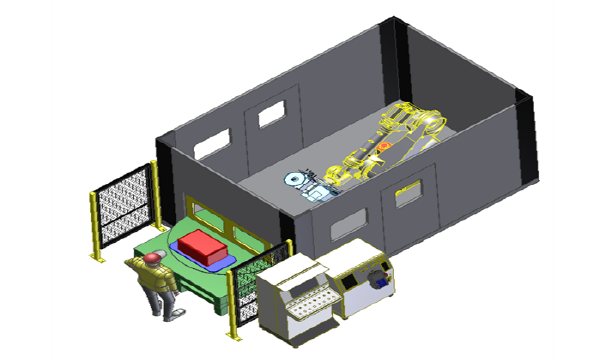
▲ 로봇시스템의 레이아웃
표준 공정 모델의 로봇자동화 시스템은 6축 수직다관절 로봇, 절단툴, 로봇베이스, 주조품 지그 및 포지셔너, 주조품 투입/취출 장치, 제어반, 로봇 보호가이드/펜스 등으로 이뤄져 있다. 작업은 주조품 인덱스 지그 투입 → 인덱스회전 → 주조품 후가공 사상(로봇) → 주조품 인덱스 회전 → 배출 순으로 진행된다.
◆ 바이오/화학 분야 표준공정 모델
◊바이오/의료기기 검사/이송 공정
바이오/의료기기 검사/이송 공정은 바이오/의료기기 포장공정 밸리데이션에 대한 GMP 국제 의료기기 지침서를 바탕으로, 검사/이송 공정에 대해서 협동로봇을 활용해 수작업 공정을 대처하고, 품질 및 생산비 절감 등을 실현하는 공정이다.
이 공정 개발이 필요한 이유는 ▲불량 발생 시 제품의 이력 확인 불가 ▲수작업 기반 병목현상으로 작업효율 저하 및 생산성 악화 ▲작업자의 숙련도 차이에 따른 후가공 품질의 편차 발생 ▲고숙련 인력수급 어려움 ▲의료기기 검사 시, 장시간 앉은 자세로 신체적 부담, 눈의 피로도 높음 등 우려가 있기 때문이다. 로봇자동화 시스템의 도입으로 ▲제품 품질 향상 제품 품질 균일화 ▲검사 정확성 향상 ▲제품 이종 혼입 방지 ▲작업자 근골격계 질환 예방 등 효과를 기대할 수 있다.
표준 공정 모델의 핵심 기능은 ▲6 미러(mirror)를 이용한 표면 검사 ▲로봇의 진공 픽업 툴로 제품 손상 없이 픽업 ▲비전 시스템을 이용한 제품의 측정/분류 시스템 ▲로봇의 효율적 움직임으로 빠른 검사 진행 등이다.

로봇시스템은 가반하중 5kg 이하 산업용 로봇, 그리퍼, 비전장치, 바코드 스캔장비, 제어기, 안전 설비 등으로 구성된다.
작업은 원소재 → 가공 → 블라스팅 → 에칭 → 자동에칭/표면 검사 → 세척 → 자동 이송 → 1차 조립 → 완제품 조립 → 최종 검사 → 포장 순으로 이뤄진다.
◊바이오/의료기기 화학소재 이송 검사공정
바이오/의료기기 화학소재 이송 검사 공정은 바이오/화학 소재의 이송/검사에 대해서 산업용 로봇을 활용하여 수작업 공정을 대처하고, 품질 및 생산비 절감 등을 실현하는 공정이다.
이 공정 개발이 필요한 이유는 ▲검사 수작업으로 제품 혼입 및 누락 발생 ▲불량 발생 시 제품의 이력 확인 불가 ▲작업자의 숙련도 차이에 따른 후가공 품질의 편차 발생 ▲고숙련 인력수급 어려움 ▲화학 소재 검사 시, 장시간 앉은 자세로 신체적 부담, 눈의 피로도 높음 등 문제가 있기 때문이다. 로봇시스템 도입으로 ▲제품 품질 향상 ▲제품 품질 균일화 ▲검사 정확성 향상 ▲제품 이종 혼입 방지 ▲작업자 근골격계 질환 예방 등 효과를 기대하고 있다.
표준 공정 모델의 핵심 기능은 ▲충진 후 제품 검사 ▲제품의 물성 및 형상에 따른 그립 방식 ▲비전시스템을 이용한 제품의 측정/분류 시스템 ▲검사, 포장, 적재 공정의 로봇 적용 등이다.
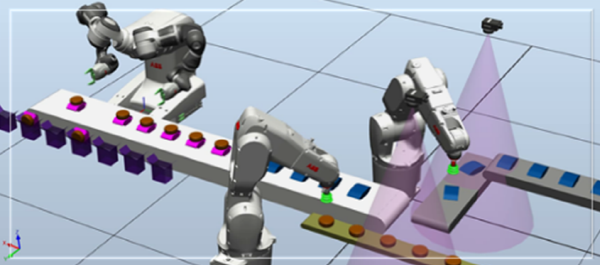
로봇시스템은 가반하중 5~130kg의 산업용 로봇, 그리퍼, 비전장치, 바코드 스캔장비, 라벨러, 정렬장치, 제어기 등으로 구성된다.
작업은 소분 → 용기공급 → 용기세척 → 충진 → 캡공급 → 캡조립 → 중량검사 → 용기착인 → 검사(외관 및 착인) → 케이스 포장 → 케이스 착인 및 라벨 부착 → 박스포장 → 팔레트 적재 → 출하 등 순으로 진행된다.
◊세포배지 교체/배양 공정
세포배지 교체/배양 공정은 세포계대배양 공정에서 다관절 로봇을 투입하여 계대배양 품질의 재현성 확보, 생산성 향상 및 생산비 절감 등을 실현하는 공정이다.
이 공정 개발이 필요한 이유는 ▲GMP 시설 내 세포 관찰 및 배지교환 등 단순반복 작업을 위해 많은 인원, 시간, 비용 발생 ▲실시간 세포 상태에 따른 적절한 공정 처리의 어려움 ▲수작업 기반 병목현상으로 작업효율 저하 및 생산성 악화 ▲작업자의 숙련도 차이에 따른 실험 결과 및 제품 품질 편차 발생 ▲고숙련 인력 수급 어려움 ▲작업자의 오류와 부주의로 인한 오염 가능성 ▲소모품 쓰레기 처리 등 환경문제 및 비용발생 등 문제가 있기 때문이다. 로봇자동화 시스템 도입으로 ▲작업환경 개선 ▲생산성 향상 ▲인건비 절감 ▲품질 안정화 등 효과를 기대하고 있다.
표준공정 모델의 핵심 기능은 ▲플라스크 및 튜브를 파지할 수 있는 그리퍼 ▲용액 분주를 위한 디스팬서 ▲디스팬서 및 그리퍼를 교체하며 사용할 수 있게 하는 툴체인저 ▲비전 센싱을 이용한 세포제외 추출 등이다.
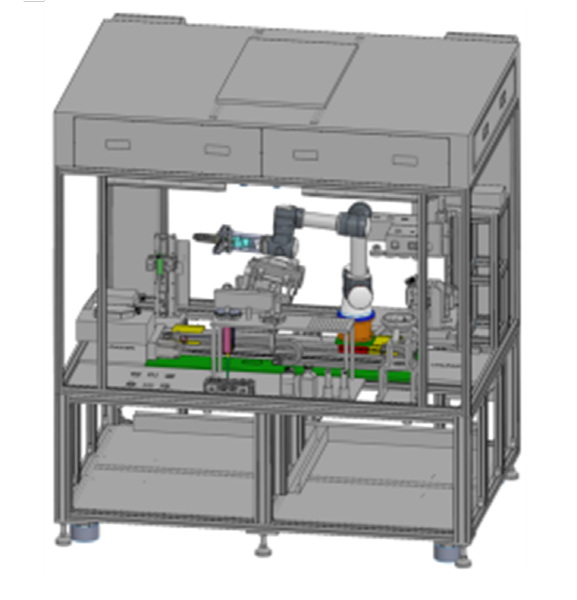
로봇자동화 시스템은 6축 수직다관절 로봇, 그리퍼, 디스펜서, 로봇베이스, 지그 및 포지셔너, 클린벤치, 제어반, 안전설비 등으로 이뤄진다.
작업은 셀 시딩(Cell Seeding) → 세포배양 및 배지교체 → 세포 탈착 → 셀 스플릿(Cell Split) → 2차 세포배양 등 순으로 진행된다.
◆ 로봇-장비 분야 표준공정 모델
◊ 다관절로봇 활용 복합사출성형 공정
다관절로봇 활용 복합사출성형 공정은 인서트 삽입 사출공정에서 수작업 공급 및 배출 검사 작업을 자동검사 및 로봇자동화 시스템으로 대체하는 것이다. 가공품의 인서트, 사출, 검사, 배출의 과정을 자동화 시스템으로 전환함으로써 생산성을 제고할 수 있다.
이 공정 개발이 필요한 이유는 ▲수작업시 생산량 편차 발생 ▲단순 반복 작업으로 인한 작업자 피로도 누적 ▲사출공정에 의한 작업장의 오염 등 문제가 있기 때문이다. 로봇시스템 도입으로 ▲검사 정확성 향상 ▲생산비 절감 및 생산성 향상 ▲작업자 근골격계 질환 예방 ▲지능화, 자동화에 의한 인건비 절감 등 효과를 기대하고 있다.
표준공정 모델의 핵심 기능은 ▲인서트 삽입을 자동화로 사출기에 안정된 인서트 ▲사출 완제품을 비전을 이용하여 칫수, 형상, 미성형 감지 ▲중량 테이터 수집에 의한 이상 감지 및 자동 제어 ▲팔렛트체인저 방식의 인서트 및 완제품 투입, 배출 자동화 등이다.

▲로봇시스템의 레이아웃
로봇자동화 시스템은 6축 다관절 로봇, 비전시스템, 지그, 다제품 대응 그리퍼, 볼피더기 정렬장치, 적재 박스 공급/배출 컨베이어, 제어기, 안전 설비 등으로 구성돼 있다.
작업은 인서트 트레이공급 → 정렬 → 인서트 삽입 및 취출(로봇) → 중량 및 비전 검사(로봇) → 조건 피드백 → 검사 제품 트레이 배출(로봇) → 트레이 배출부 리프터 적재 순으로 이뤄진다.
◊ 세척장비 로봇 시스템 공정
세척장비 로봇 시스템 공정은 대형 항공 부품 금형에 오염물질 제거를 위한 수작업 세척 공정과 이형제 도포 공정의 자동화를 위해 로봇 시스템을 도입하여 작업자의 안전과 생산성, 품질 안정을 확보하기 위한 모델이다. 오토클레이브 성형 후 금형에 부착된 경화 레진, 오염물 제거 및 이형제 적용 공정으로서 로봇 시스템을 적용한다. 시뮬레이션을 통해 공정의 최적 조건 탐색 및 이상 유무를 판단하는 기능을 추가했다.
이 공정 개발이 필요한 이유는 고중량 대형 부품의 세척/이형제 도포 공정을 수작업으로 진행함에 따라 부품의 낙하로 인한 작업자 부상 위험과 해당 공정에서 사용되는 유독 화학 물질로부터 작업자가 노출되는 문제가 발생하기 때문이다. 또한 세척/이형제 도포 작업과 검사 공정이 수작업으로 진행됨에 따라 작업자의 피로도 증가, 수작업에 따른 제품 부분공정 누락, 품질 부분 불량으로 다음 공정 불량 원인을 제공하는 것으로 지적되고 있다. 로봇시스템 도입시 ▲작업자 근골계, 호흡기 질환 예방 ▲지능화, 자동화에 의한 인건비 절감 ▲생산성 향상 등 효과를 기대할 수 있다.
세척장비 로봇 시스템 공정의 핵심 기능은 ▲고중량 부품 대상 안정적인 작업을 위한 작업공간 설계 ▲1대의 로봇으로 다수 임무를 처리하는 엔드이펙터 설계 ▲공정 데이터 수집으로 이상 감지 및 공정 조건 탐색 등이다.

▲ 로봇시스템의 레이아웃
로봇시스템은 6축 다관절 로봇, 드라이 아이스 블라스터, 샌딩, 이형제 도포도구, 제어반 등으로 구성된다.
작업은 금형 턴테이블에 진입/고정 → 로봇 세척 공정 수행 → 로봇 이형제 도포 공정 수행 → 최종 검사 등 순으로 진행된다.
◊ 미니 스텐트 금형 자동화 공정 로봇-장비 모델
미니 스텐트 금형 자동화 공정은 인체 내의 막힌 곳에 넣어 혈액, 체액, 음식물 등의 이동 경로를 확보하는 데 쓰이는 스텐트의 제조 공정에서 철심(핀) 삽입 및 접착 검사 작업을 자동화해 생산성, 품질, 안정성을 확보하기 위한 것이다.
이 공정 개발이 필요한 이유는 작업자의 숙련 정도에 따라 생산성과 품질의 차이가 발생하고, 인력 부족과 작업 기피 현상이 심화되고 있기 때문이다. 품질 불량 발생시 금형을 전량 폐기하거나 다시 만드는 과정에서 시간이 많이 걸린다. 수작업 교육시 기술 유출도 우려된다. 로봇자동화 시스템 도입으로 생산비 절감, 생산성 향상, 지능화, 인건비 절감 등 효과를 기대할 수 있다.
미니 스텐트 금형 자동화 공정의 핵심 기능은 ▲배지교체 공정 중의 오염 방지 ▲자동화 진행중 배지교체 전/후 안정된 세포관찰 ▲데이터 수집에 의한 이상 감지 및 자동 제어 등이다.

▲ 공정의 구성도
로봇시스템은 6축 로봇, 그리퍼, 비전시스템, 3축 및 4축 직교로봇, 핀의 본딩 및 삽입 장치, 안전시스템 등으로 구성된다. 작업은 스텐트 지그 공급(로봇) → 지그 홀가공(장비) → 세척 및 검사(장비) → 핀 삽입(장비) → 완제품 검사(장비) → 완제품 배출(로봇) 순서로 진행된다.
◊ 선박 철의장품의 다품종 유연생산을 위한 아크용접 로봇-장비 모델
선박 건조 시 사용되는 철의장품(pipe support)는 척당 7000~9000여개가 사용되며, 선박의 선종 및 선형에 따라 제품 형상, 크기, 중량이 매우 다양하다.
선박 철의장품 다품종 유연생산을 위한 아크용접 공정은, 수작업에 의존하는 용접 공정에 대해 3D 비전 카메라와 3D 부품 도면 데이터를 이용하여 실제 환경에서의 용접 경로 오차와 용접 공정 파라미터를 자동 보정하여 용접을 수행하고, 용접 이후에 용접 비드 자동 검사가 가능한 로봇 기반의 용접 공정과 그 시스템을 의미한다.
이 공정은 현재 수용접에 의해 전량 철의장품을 제작하고 있어 작업자의 상태 및 스킬에 따라 용접 품질 편차 및 생산량 변동이 발생한다. 용접 작업자가 부재 이동 및 용접을 모두 수행하기 때문에 부재에 깔림, 협착 등의 산업재해 위험이 존재하며, 용접 작업 시 집중력 하락으로 용접 품질 불량이 발생할 수 있다. 용접 작업자는 고령화되고 있으며, 3D 직종이라는 인식으로 작업자의 확보가 어려운 상황이다. 로봇 자동화 시스템 도입시 ▲철의장품 작업 효율 및 생산성 향상 ▲지능화 및 자동화를 통한 인건비 절감 ▲용접 불량률 감소 ▲용접 인력 부족 문제 해소 ▲산업재해 감소 및 근로 환경 개선 등 효과를 기대할 수 있다.
선박 철의장품 다품종 유연생산을 위한 아크용접 로봇-장비 모델의 핵심 기능은 ▲피용접물의 용접용 로봇 ▲용접물 부재 핸들링 로봇 ▲용접물 인지 및 용접선 자동 교시를 위한 3D 비전 카메라 ▲용접품질 검사를 위한 3D 비전 카메라/레이저 비전 센서 ▲용접ㆍ핸들링 로봇 및 부재 이동용 컨베어벨트/비전 카메라 간의 인터페이스 등이다.

▲ 로봇시스템 레이아웃
로봇시스템은 용접 및 부재 이동용 핸들링 로봇, 3D 비전 카메라 기반 용접선 자동 교시 장치, 3D 비전 카메라/레이저 비전 센서 기반 아크 용접부 검사 장치, 용접물 고정 턴테이블 지그 장치, 용접 부재물 이동 컨베어벨트 장치, 클라우드 기반 용접 상태를 통합한 모니터링 시스템 등으로 구성된다.
작업은 용접 라인 투입(로봇) → 매그(MAG) 용접(로봇) → 용접 제품 언로딩(로봇) → 용접 합/불 검사(로봇) → 합/불 제품 구분하여 팔레트 적재(로봇) → 다음 공정 이동(사람) 순으로 이뤄진다.
장길수 ksjang@irobotnews.com
<저작권자 © 로봇신문사 무단전재 및 재배포금지>
'산업용로봇' 카테고리의 다른 글
레인보우로보틱스, KAI 차세대 전투기에 협동로봇 드릴링 시스템 투입 (0) | 2024.03.15 |
---|---|
스위스 ABB, 미국 미시건주에 로봇 제조 시설 재단장 오픈 (0) | 2024.03.15 |
화낙, '모덱스 2024'에 AI 머신 비전 기반 로봇 선봬 (1) | 2024.03.06 |
美 콘 에디슨-ULC테크놀로지스, 전력선 연결 자동화 머신 개발·테스트 (1) | 2024.03.05 |
[기획] 리뷰-2023 제조로봇 실증사업(3) (1) | 2024.03.04 |